ハンマリング試験で測定できる数値とは?他の試験との違いや現場での活用例までを徹底解説
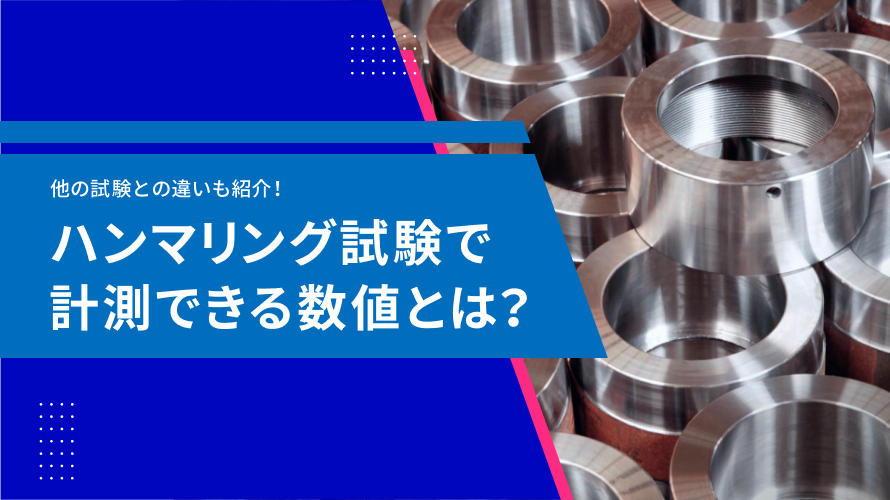
目次
ハンマリング試験とは?手法の概要や他の試験との違いを解説
振動や異音が製品や設備の品質に影響する場面は少なくありません。そんなとき、製品や構造物の「固有の振動特性」を調べるために使われるのが、ハンマリング試験です。
この試験は、製品や構造物の表面を小さなハンマーで打撃(インパルス)し、振動の応答を記録・解析することで、振動モードや固有振動数、減衰比といった重要な物理量を導き出す手法です。
ハンマリング試験は、以下のような特徴があります。
- 構造物に外力を与えるだけで、比較的簡便に実施できる
- 測定器具がコンパクトで、現場での持ち運びやすい
- 試験対象が動作中でなくても測定可能(静的状態でOK)
本章では、まずハンマリング試験の概要と目的を確認し、類似の振動試験との違いについても理解を深めていきましょう。
ハンマリング試験の概要と目的
ハンマリング試験は、構造物の固有振動特性を「叩いて」知るための手法です。専用の加振用ハンマー(インパルスハンマー)で対象物を叩き、その反応(加速度など)をセンサーで記録して、FFT(高速フーリエ変換)で周波数成分に変換し、構造の特性を把握します。
目的として代表的なものは次のとおりです:
- 製品や設備の共振周波数(固有振動数)の把握
- 構造の剛性・柔軟性の評価
- 振動原因の調査と異音対策
- FEMモデルとの整合確認や設計改善の検証
ハンマリング試験は、静的な状態でも実施可能なため、実稼働前の開発段階でも活用されることが多く、試作段階での異音対策や、工場設備の診断にも幅広く利用されています。
※ハンマリング試験の基礎知識やメリット・デメリットについては、こちらの記事で詳しく解説しています。
FEM:FEM(Finite Element Method/有限要素法)とは、構造物を細かな要素に分割し、それぞれの応力や変形を数値的に解析する手法です。設計段階での振動予測や強度評価に広く利用されています。
他の振動試験との違いとは?
ハンマリング試験は、シンプルかつ効果的な振動評価手法ですが、他にも振動に関する検査は多く存在します。それぞれの手法には得意・不得意があるため、目的に応じた使い分けが重要です。
ここでは、加振試験、応力・破壊検査、非接触測定と比較しながら、ハンマリング試験の特徴を見ていきましょう。
試験方法 | 試験対象 | 特徴・強み | わかること |
---|---|---|---|
ハンマリング試験(打撃試験) | 機械構造物、設備、部品、板材など | 準備が簡単 装置がコンパクト 非破壊で実施可能 |
固有振動数、減衰特性、構造健全性 |
加振試験 | 精密機器、電子部品、航空部材など | 周波数掃引が可能 外部振動に対する耐性評価に最適 疲労評価にも対応 |
共振点、応答変位、耐久限界 |
応力測定/破壊試験 | 金属・樹脂素材、接合部、構造体 | 材料の力学特性を直接数値化 破断点や最大応力を明示 |
応力・ひずみ分布、破壊特性、強度限界 |
非接触振動測定 | 微小構造物、高速振動体、光学系 | 高精度・非接触 微細な変位の可視化 干渉なし |
微細振動の振幅・周波数、表面挙動の可視化 |
表からもわかるように、ハンマリング試験は他の試験方法に比べて準備が簡易で、設備やコストの負担が少ない点が特徴です。特に、固有振動数や減衰特性といった振動特性の把握を目的とした初期評価や、現場でのトラブルシュートに向いています。一方で、加振試験や応力試験のように長時間にわたる耐久性評価や負荷試験には不向きです。非接触振動測定は精密かつ連続的なデータ取得が可能ですが、測定機器が高額になるケースもあります。試験目的や設備環境に応じて、最適な手法を選択することが重要です。
ハンマリング試験で「わかること」
ハンマリング試験では、構造物に軽く打撃を加えることで、振動応答データを取得します。そこから、構造の内部に隠れていた「性質」や「問題の原因」が浮かび上がってきます。この章では、試験で得られる3つの代表的な物理量について解説します。
確認できる主な指標は以下の3つです。
- 固有振動数(構造物が自然に振動する周波数)
- 減衰比(どれだけ速く振動が収束するか)
- 振動モード(どのように振動するかのパターン)
それぞれの物理量が何を意味し、どのような目的で使われるのかを順に見ていきましょう。
固有振動数の測定
固有振動数とは、その構造体が外力を加えなくても自然に振動しようとする周波数のことです。人間に例えるなら、「声のトーン」のようなもので、形状や材質によって決まります。
ハンマリング試験では、打撃を加えたあとに得られた応答波形を周波数解析することで、ピークを持つ周波数=固有振動数を特定できます。
この情報は次のような場面で役立ちます:
- 共振のリスク評価:動作中の回転体が固有振動数と一致すると、異常な振幅が発生(共振)し、破損リスクが高まる
- 設計の妥当性確認:想定した剛性・質量バランスが製品に反映されているかを検証
- 製品間のバラツキ検出:同一モデルでも組付け条件により固有振動数に差が出る場合がある
固有振動数は、製品の健全性や一致性を判断する上での基準値となる重要な指標です。
減衰比の測定
減衰比は、構造が受けた振動をどれだけ早く静止させるか(収束させるか)を示す値です。わかりやすく言えば「音の余韻」のようなもの。試験では、振動波形の減衰具合から計算します。
測定結果から次のような情報が得られます:
- 異常の予兆検出:減衰が早すぎる・遅すぎる場合、部品の劣化や締結不良の可能性がある
- 吸音材やダンパーの効果検証:減衰率の変化で部材追加の効果を定量評価できる
- 快適性の評価:電子機器や家電などで、不要な振動が短時間で収束することが品質と関わる
特に、製品の長寿命化・静音化を目指す場合、減衰特性の把握は欠かせません。
振動モードの可視化
振動モードは、構造物がどのように揺れるか(形の変化パターン)を示す情報です。図やアニメーションで表示すると、どの部分が大きく動いているか、節点(動かない点)がどこかが明確になります。
これにより、以下のような分析が可能になります:
- 異常振動の発生箇所の特定
- 構造上の弱点(応力集中箇所)の予測
- 設計段階での補強検討や剛性改善の判断材料
たとえば、「あるボルトの緩みで特定部位だけが大きく揺れていた」などの実態が、振動モードを見れば一目瞭然です。CADモデルとの重ね合わせにより、FEM解析との整合性も確認できます。
ハンマリング試験の試験結果はどう活用されるのか?
ハンマリング試験で得られた振動データは、単なる波形ではありません。振動特性を数値化することで、製品や設備の開発・保守・改善に幅広く活用できるのです。この章では、試験結果の代表的な活用シーンを4つに分類して紹介します。
ハンマリング試験の結果が活用される主な場面は以下の通りです。
- 設計・開発段階での構造最適化
- 生産現場での品質管理とばらつき確認
- 出荷判定・納品検査での活用
- 異常診断や予防保全の精度向上
それぞれの活用方法について、実際の業務と結びつけながら見ていきましょう。
設計・開発段階での構造最適化
ハンマリング試験は、試作段階の製品に対して構造上の課題を可視化するために活用されます。例えば、設計通りの剛性が確保されているか、共振しやすい箇所はどこか、余分な振動を誘発していないか。これらは図面だけでは判断できません。
試験で得た固有振動数やモード形状をもとに、次のような設計改善が可能になります:
- 部材の厚みや補強リブの追加設計
- ネジ・締結部の位置調整
- 材質変更やダンパーの導入検討
生産現場での品質管理とばらつき確認
量産品においては、部品ごとにわずかな製造誤差や組付け条件の違いが生じます。ハンマリング試験は、それによって生まれる「性能のばらつき」を定量的に確認する手段として用いられています。
たとえば、以下のような確認ができます:
- 設計値通りの固有振動数に収まっているか
- 異常に高い(または低い)周波数を持つ個体が存在しないか
- 減衰特性に極端な差が出ていないか
このようなデータを蓄積することで、不具合予兆の早期発見につながります。
出荷判定・納品検査での活用
特定の規格や仕様が求められる製品(例:自動車部品、医療機器、精密装置)では、最終検査としてハンマリング試験を導入するケースもあります。
- 固有振動数の範囲チェック
- 振動モードの一致性確認
- NG品(締結不良・変形・部品欠損など)の選別
このような合否判定を加えることで、品質の信頼性を確保できます。また、ハンマリング試験は非破壊検査です。その特性から、製品を壊さずに状態を把握できるという利点もあります。
異常診断や予防保全の精度向上
運用中の設備や装置に対して、定期的にハンマリング試験を行うことで、構造の劣化や異常兆候の診断が可能になります。
例としては次のような診断が可能です:
- 過去の振動データと比較し、固有振動数の変化を検出
- 減衰率の低下により、締結の緩みや部品摩耗を推定
- 振動モードの変化から、構造歪みや応力集中を可視化
こうしたデータに基づく予防保全は、突発的なライン停止の防止につながることから、製造現場の信頼性向上に寄与します。
ハンマリング試験が役立つ現場や製品の例
ハンマリング試験は、構造物の振動特性を可視化できる非破壊評価手法として、幅広い分野で実用されています。特に、共振の影響が無視できない製品や設備において、設計・検査・保守の各段階で大きな役割を担っています。ここでは、ハンマリング試験が活躍する現場と、その対象となる製品例を紹介します。
- 自動車部品:剛性・共振特性の確認
車体フレーム、サスペンション、ドア、エンジンマウントなどの部品では、走行時に生じる振動や騒音を制御するため、共振モードや固有周波数の分析が不可欠です。ハンマリング試験を実施することで、共振点の分布や振動伝播の傾向を把握し、設計の改良やNVH対策に反映できます。 - NVH対策:NVHとは「Noise(騒音)・Vibration(振動)・Harshness(不快感)」の頭文字を取った用語で、自動車の快適性や静粛性を評価・改善する際に使われる指標です。NVH対策とは、それらを抑えるための一連の設計・評価・改善施策を指します。
- 航空機・鉄道車両:軽量構造の健全性評価
航空機の翼や機体、鉄道車両の台車やボディは、高剛性かつ軽量という相反する要件を満たす必要があります。ハンマリング試験は、製造後の品質確認やメンテナンス時の異常検知に有効であり、構造健全性を非破壊で素早く評価できる手法として定着しています。 - 精密機器:振動感度の事前評価
半導体装置、光学計測装置、検査用ロボットなど、高精度を要する機器は微細な振動にも敏感です。設計段階でハンマリング試験を用いれば、共振しやすい部位や固有モードを把握でき、防振構造やアイソレーターの配置に根拠を持たせることが可能です。
- 工場設備:劣化や異常の兆候検知
搬送装置、貯蔵タンク、支持架台など、稼働年数の長い工場設備においても、定期的なハンマリング試験が有効です。振動モードの変化から構造の緩みや剛性低下を捉えられるため、計画的な保守や更新判断に活用されています。
今、ハンマリング試験が注目されている理由
近年、製造現場やインフラ管理の現場では、点検・診断の効率化と低コスト化が強く求められています。その中で、従来から存在するハンマリング試験が、改めて注目を集めています。新たな技術革新の影に隠れがちな手法ですが、現在の社会的・産業的なニーズに見事にフィットしているからです。ここでは、ハンマリング試験が再評価されている背景を3つの観点から整理します。
ハンマリング試験が注目されている理由1. 点検・保全の省人化トレンドとの親和性
製造業の現場では、熟練作業者の高齢化や人手不足が深刻な問題です。多くの企業において、「いかに少人数で、確実な点検を実施できるか」が重要なテーマになっています。ハンマリング試験は、センサーとハンマーがあれば1人でも実施できるうえ、短時間で多くの項目を確認できます。
特に、定期保全ではなく予防保全の考え方が浸透している現在、機器や構造物の健全性を簡易的に判断できる手法は重宝されます。音や振動のデータを蓄積することで、異常傾向を数値で捉えられるようになり、保守の判断材料としても使いやすくなっています。
ハンマリング試験が注目されている理由2. IoT・デジタルツイン時代における軽量・安価な測定手法
IoTやデジタルツインの導入が進む一方で、すべての設備に高価なセンサーを常設するのは非現実的です。そこで、スポット的にデータを取得できるハンマリング試験が、補完的な手段として見直されています。
ハンマリング試験は、持ち運びが容易な計測器と加振用ハンマーがあれば実施可能であり、設備への後付け工事が不要です。取得したデータをクラウドに送信し、時系列での変化を追跡するなど、ITとの親和性も高くなっています。
このように「簡易かつ即時に測れる」「データ連携しやすい」といった特性は、デジタル化と相性がよく、導入のハードルが低い利点として再評価されています。
ハンマリング試験が注目されている理由3. インフラ・老朽設備への適用拡大
老朽化が進む社会インフラの点検においても、ハンマリング試験は重要な選択肢となっています。橋梁・水道管・プラント配管など、外観からは判断しづらい内部の異常や空洞を、打音や振動応答から推定できるからです。
特に、打撃に対して応答の変化を解析する非破壊検査として、目視や打音検査のような経験則に頼らず、定量的な評価ができる点が評価されています。
さらに、ハンマリング試験は対象物に直接打撃を加えるため、表面だけでなく内部構造の健全性を推定するヒントが得られます。特殊な環境下でも比較的柔軟に対応できるため、現場に合わせた応用が進んでいます。
ハンマリング試験の導入支援や設備開発については、TMCシステムにご相談ください
ハンマリング試験は、設備や構造物に打撃を加えて振動応答を解析することで、内部の状態や構造的な特性を把握できる簡便な測定手法です。特別な設備や専門知識がなくても導入しやすく、製造ラインの予知保全から、インフラの健全性確認まで、幅広い現場で活躍しています。
とくに近年では、以下のような点から再評価されています。
- 少人数で実施可能な簡易性と即応性
- IoT・デジタルツイン時代に適した軽量データ取得
- インフラや老朽設備の非破壊・簡易診断ニーズとの適合
ハンマリング試験は「省人化」「低コスト化」「簡易導入」といったトレンドと高い親和性を持ち、今後も多くの現場で活用が進むと考えられます。
ハンマリング試験を現場で安定して行うためには、「加振の再現性」や「操作性」も重要な要素です。特に、現場ごとに作業者が異なる場合や、測定データの信頼性が問われる場面では、誰でも安定した加振ができる機器の導入が効果を発揮します。TMCシステムが提供する定量加振機インパルスハンマ版は、熟練者に頼らずとも再現性の高い加振を実現し、データ取得の信頼性向上に寄与します。
またTMCシステムでは、ハンマリング試験に関する装置やシステム導入のご相談を承っております。現場の課題に応じた導入支援や、計測システムのカスタマイズにも対応しています。「自社で活用できるのか?」「今ある設備で試せるのか?」といった疑問があれば、お気軽にお問い合わせください。