突発的な機械故障を防ぐ!最新の予兆検知技術と予知保全の連携によるダウンタイム削減策
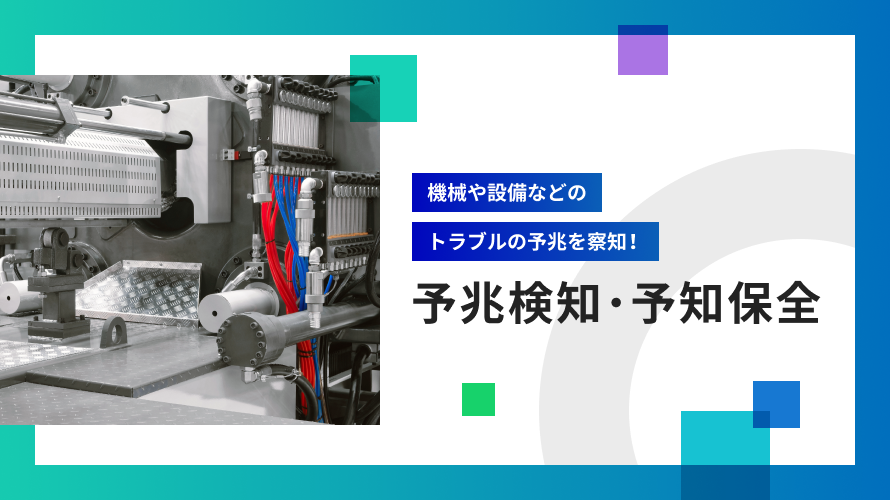
予兆検知と予知保全は、現代の製造業における設備管理において重要な役割を果たします。本記事では、予兆検知と予知保全の基本概念について紹介し、製造業におけるその重要性を説明します。
目次
予兆検知とは
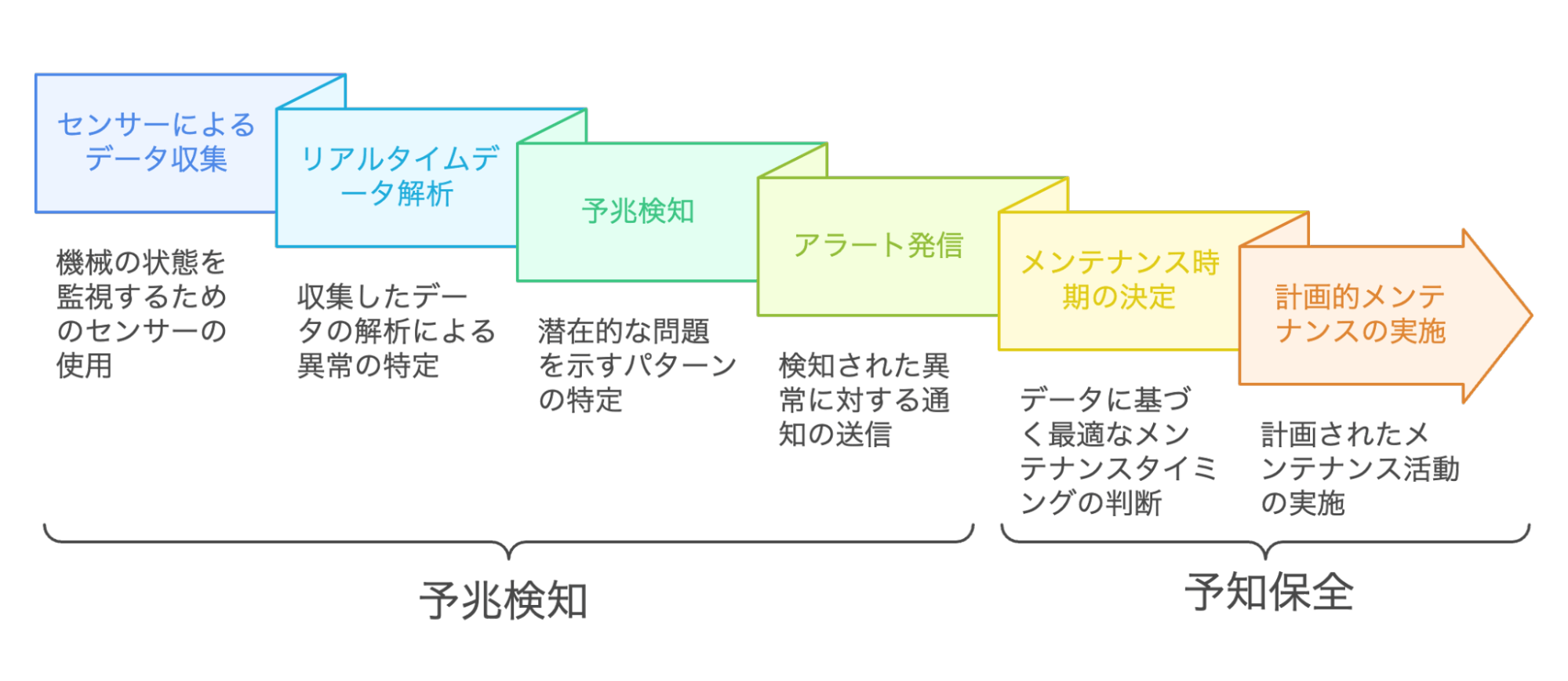
予兆検知は、設備や機械の異常を未然に察知し、早期対処を可能にする技術です。設備の状態をリアルタイムで監視することで、潜在的な問題を早期に発見し、突発的な故障を防ぎます。異常の前兆を捉えることが目的であり、具体的な対処方法の決定は予知保全の領域となります。
この技術の中核となるのが、各種センサーによるデータ収集です。設備の動作状態を常時モニタリングします。これらのセンサーが捉えた細かな変動から、異常の兆候を早期に検出します。収集したデータは、専用の分析ソフトウェアでリアルタイムに解析されます。機械学習アルゴリズムや統計解析を用いて異常パターンを特定し、問題が検知された際には即座にアラートを発信します。このプロセスにより、生産ラインのダウンタイムを大幅に削減できます。
予知保全とは
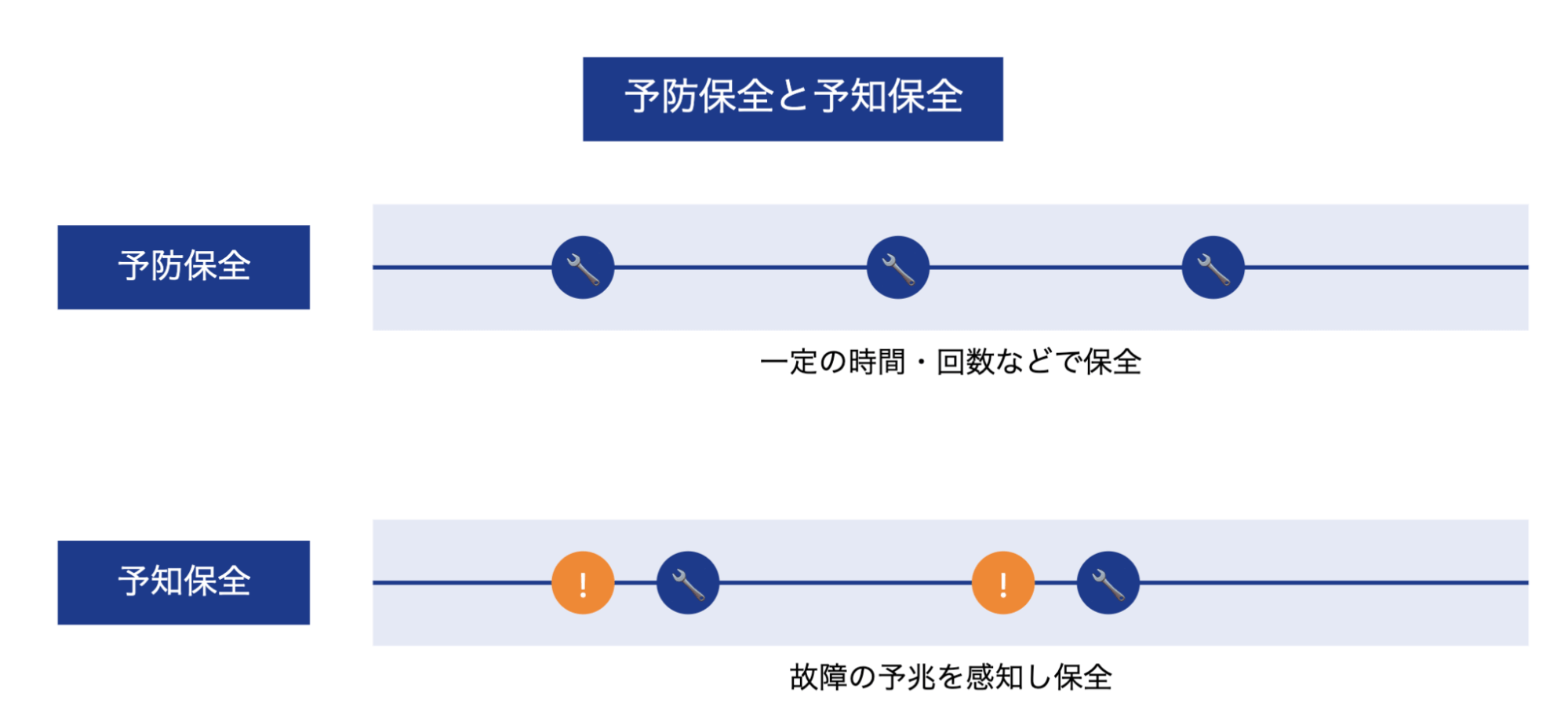
予知保全は、設備の状態を常時監視し、データに基づいて最適なタイミングでメンテナンスを実施する先進的な保全手法です。従来の定期的な保全とは異なり、実際の設備状態に応じて保守を行うため、より効率的な設備管理が可能となります。 類似の仕組みとして予防保全がありますが、予防保全は、故障を未然に防ぐため、定期的なスケジュールに基づいてメンテナンスを実施する手法です。部品の寿命や使用時間などから、画一的に保全時期を決定します。予知保全は設備の実際の状態データを分析し、個々の設備に最適なタイミングで保全を行います。これにより、過剰な保全作業を避けながら、必要な時期に必要な保全を実施できます。 予兆検知で収集・分析したデータから、最適なメンテナンス時期を判断し、計画的な保全活動を実施します。これにより、突発的な故障を防ぎ、生産性の維持・向上を実現します。結果として、ダウンタイムの削減とメンテナンスコストの最適化を同時に達成します
予兆検知と予知保全の連携強化
両システムの連携により、異常の検知から保全実施までをシームレスに実現します。この連携を効果的に機能させるためには、まず基盤の整備が必要です。共通のデータプラットフォームを構築し、センサーデータを標準化することで、リアルタイムな情報共有が可能になります。
データ活用の最適化も重要な要素です。センサーから収集したデータは両システム間でリアルタイムに共有され、予兆検知で捉えた異常の兆候は予知保全の計画立案に即座に反映されます。さらに、AIによる分析を活用することで、より正確な予測と適切な保全時期の決定が可能になります。
効果的な運用には、組織体制の整備も欠かせません。部門間の連携を強化し、明確な判断基準を設定することで、検知から保全実施までの一連のプロセスがスムーズに機能します。各担当者の役割と責任を明確にすることで、迅速な意思決定と対応が可能となります。
このような連携により、異常の早期発見と迅速な対応が実現し、保全計画の最適化とダウンタイムの大幅削減が期待できます。さらに、メンテナンスコストの適正化にも貢献します。実例として、製造業A社では両システムの連携により、設備故障を20%削減し、保全コストを30%削減することに成功しています。
予兆検知・予知保全システム設計の重要ポイント
効果的なシステム設計には、3つの重要な要素があります。センサーの選定・配置、データ基盤の構築、そしてアラート体制の確立です。これらを適切に組み合わせることで、高精度な異常検知と効率的な保全が実現します。
センサー選定と配置
センサーは故障の予兆を捉える「目」となります。対象設備の特性に応じて適切なセンサー種類を選定し、異常が発生しやすい箇所に重点的に配置します。設備の動作分析に基づく戦略的な配置により、効率的なデータ収集が可能になります。
主なセンサー | 収集するデータキスト |
---|---|
振動センサー | 機械の振動パターンを識別 |
温度センサー | 異常な温度上昇を察知 |
電流センサー | 異常な電流変動を検出 |
音響センサー | 異音を発見 |
データ収集と分析基盤
IoTセンサーからリアルタイムで収集したデータを、効率的に処理・分析できる基盤が必要です。収集したデータの品質管理は、システムの信頼性を左右する重要な要素となります。 収集した生データには様々な問題が含まれる可能性があります。ノイズの混入、センサーの誤作動による異常値、通信エラーによる欠損値などです。これらに対して、異常値の検出と除去、欠損値の補完、ノイズの除去とスムージング、データの正規化・標準化などを実施し、分析に適した品質を確保します。 また、収集したデータは、長期的な傾向分析や機械学習モデルの学習に活用するため、適切な形式で保存・管理する必要があります。時系列データベースの活用や、データの圧縮・アーカイブ方針の策定も重要です。
アラート体制の確立
異常検知時の迅速な対応のため、段階的なアラート体制を構築します。異常度に応じて3段階(注意・警告・緊急)のレベルを設定し、それぞれに適した通知方法を定めます。例えば、注意レベルではメール通知、警告レベルではSMS通知、緊急レベルでは電話連絡といった具合です。 また、アラート発生時の対応手順を明確化し、担当者の役割分担や連絡系統を事前に定めておくことが重要です。さらに、誤報対策として、アラートの閾値調整や複数センサーでのクロスチェックなども実施します。これらにより、確実な異常検知と迅速な対応が可能になります。
予兆検知・予知保全システムの成功事例
製造業での導入が進む予兆検知と予知保全システムは、具体的な成果を上げています。自動車メーカーAでは主要生産ラインへの導入によりダウンタイムを40%削減し、電機メーカーBでは部品交換の最適化で保全コストを30%削減しました。これらの成功の背景には、経営層の理解と現場への適切な教育・訓練があります。また、継続的なシステム評価と改善により、効果を最大化しています。 導入効果は多岐にわたります。予知保全によるダウンタイムの削減、メンテナンス計画の最適化による作業効率向上、設備寿命の延長による投資コストの抑制など、直接的なコスト削減効果が見られます。さらに、安定した設備稼働により品質向上も実現しています。電子部品メーカーCでは、メンテナンスコスト20%削減と不良率15%低減を同時に達成しました。 投資対効果(ROI)の分析では、初期投資の回収期間、年間のコスト削減額、生産性向上による売上増加などを指標として評価します。化学メーカーDの事例では、年間3,000万円のコスト削減を実現し、投資回収期間は1.5年でした。このように、適切な導入と運用により、高いROIを達成した事例もでてきています
設備の予兆検知・予知保全に関するご相談は、TMCシステムへ
突発的な機械故障でお困りではありませんか?
- センサー選定や配置の最適化方法がわからない
- データの収集・分析に課題がある
- アラート体制の構築方法を知りたい
- システムの自動化・効率化を検討している
- 予知保全との連携方法を模索している
TMCシステムでは、お客様の設備特性や運用要件に合わせた最適なシステムをご提案いたします。センサーの選定から、データ分析基盤の構築、アラート体制の確立まで、トータルでサポートいたします。まずはお気軽にご相談ください。