振動試験の基礎知識 〜製品の信頼性を確保するために必要な試験とは〜
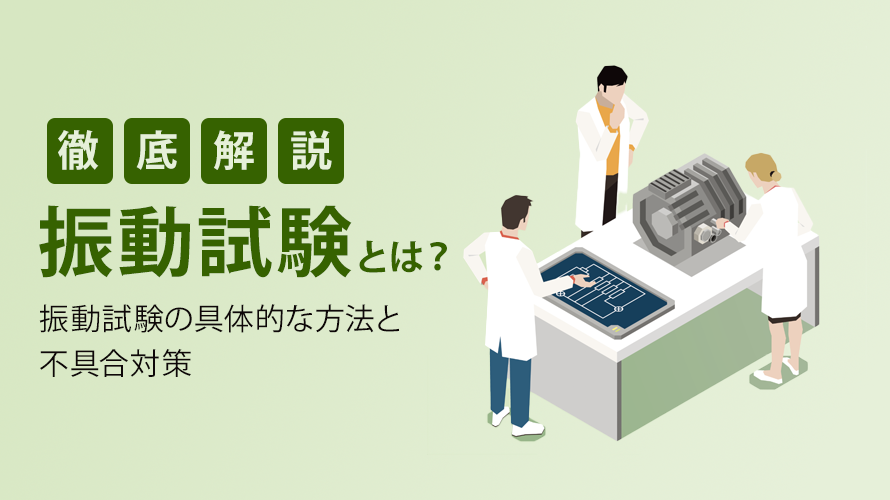
振動試験の基本とその重要性
振動試験とは?
振動試験とは、製品や材料に人工的に振動を与えることで、その耐久性や信頼性を評価する試験のことです。例えば、自動車部品では走行時の振動、電子機器では輸送時の衝撃など、製品は様々な振動にさらされます。
- 自動車のエンジンマウント:エンジン振動による疲労破壊
- スマートフォン:落下時の基板損傷
- 産業機器:設置環境での共振による緩み
これらの不具合は、製品出荷後に発見されると重大な問題につながる可能性があります。
なぜ振動試験が重要か
製品の振動による不具合は、経済的な損失だけでなく、企業の信頼を失墜させることにもつながります。最悪の場合、人命に関わる事故を引き起こす可能性も孕んでいます。振動試験を実施し、不具合を事前に予測・対策することで、安全な製品を提供し、企業の社会的責任を果たすことが求められます。
振動試験の種類と目的
振動試験には、正弦波振動試験、ランダム振動試験、衝撃試験など、様々な種類があります。それぞれの試験は異なる目的と方法を持ち、製品の用途や想定される環境に応じて適切な試験を選択することが重要です。
1)正弦波振動試験
正弦波振動試験は、製品に一定のリズムで振動を与える試験方法です。専用の振動装置を使って、上下や左右に規則正しく振動を与えていきます。音楽のメトロノームのような一定のリズムで製品を揺らすイメージです。この試験により、製品のどの部分が振動に弱いのか、また、どの程度の振動で問題が発生するのかを明確に把握することができます。 技術的な観点からみると、正弦波振動試験では周波数掃引という手法を用います。これは、低周波数から高周波数まで段階的に振動数を変化させることで、製品の共振周波数を特定する方法です。共振周波数とは、製品が最も大きく振動する周波数のことで、この周波数を把握することで、製品設計の改善や対策を講じることができます。試験では通常、5Hz から2000Hz程度の範囲で周波数を変化させ、加速度センサーを用いて製品の応答を測定します。 自動車のエンジン周りの部品や、工場で使用される機械など、一定の振動にさらされる製品の検査に広く採用されています。
- 自動車のエンジンマウント評価(エンジン振動の共振点チェック)
- 工作機械の据付評価(機械振動の影響確認)
- 電子基板の実装評価(共振による部品剥離の検証)
2)ランダム振動試験
ランダム振動試験は、不規則な振動を製品に与える試験方法です。複数の異なる振動を組み合わせてランダムな振動を作り出すことで、実際の使用環境により近い状態での製品の挙動を確認します。例えると、でこぼこ道を走る車の振動のようなイメージです。この試験では、実際の使用環境に近い条件で製品の耐久性や信頼性を確認することができます。 この試験の特徴的な点は、パワースペクトル密度(PSD)という指標を用いることです。PSDは、各周波数における振動のエネルギー分布を表すもので、単位は通常G²/Hzで表されます。試験では、実際の使用環境で測定したPSDプロファイルを再現することで、より現実的な振動環境での製品評価が可能となります。また、加速試験として、PSDレベルを上げて試験時間を短縮する手法も一般的に用いられています。 主に輸送時の振動評価や、航空機部品など、複雑な振動環境にさらされる製品の検査に使用されています。
- 輸送時の振動耐久性評価(トラック輸送時の振動再現)
- 航空機搭載機器の評価(エンジン振動・気流の影響確認)
- 建設機械の車載機器評価(不整地走行時の振動再現)
3)衝撃試験
衝撃試験は、急激な衝撃を製品に与える試験方法です。専用の装置を使って、ハンマーで叩いたときのような瞬間的な衝撃を与えます。この試験により、突発的な衝撃に対する製品の耐久性や、内部構造の堅牢性を確認することができます。 試験の実施にあたっては、製品の特性や目的に応じて適切な試験方法を選択することが重要です。例えば、フォースハンマを使用する場合、ハンマヘッドの重さと先端の緩衝材の硬さの組み合わせが重要です。この組み合わせによって、製品にどのような振動を与えられるかが決まってきます。 特にスマートフォンや家電製品など、日常的に落下や衝突のリスクがある製品の検査に多く採用されています。
- スマートフォンの落下試験(落下時の基板・筐体破損評価)
- 包装品の輸送評価(積み下ろし時の衝撃影響確認)
- 産業機器の耐震試験(地震時の挙動確認)
次に、「衝撃試験」に着目して、検査時の異常検出とその対策について説明していきます。
振動試験(衝撃試験)の不具合分析と対策
衝撃試験の分析と異常検出
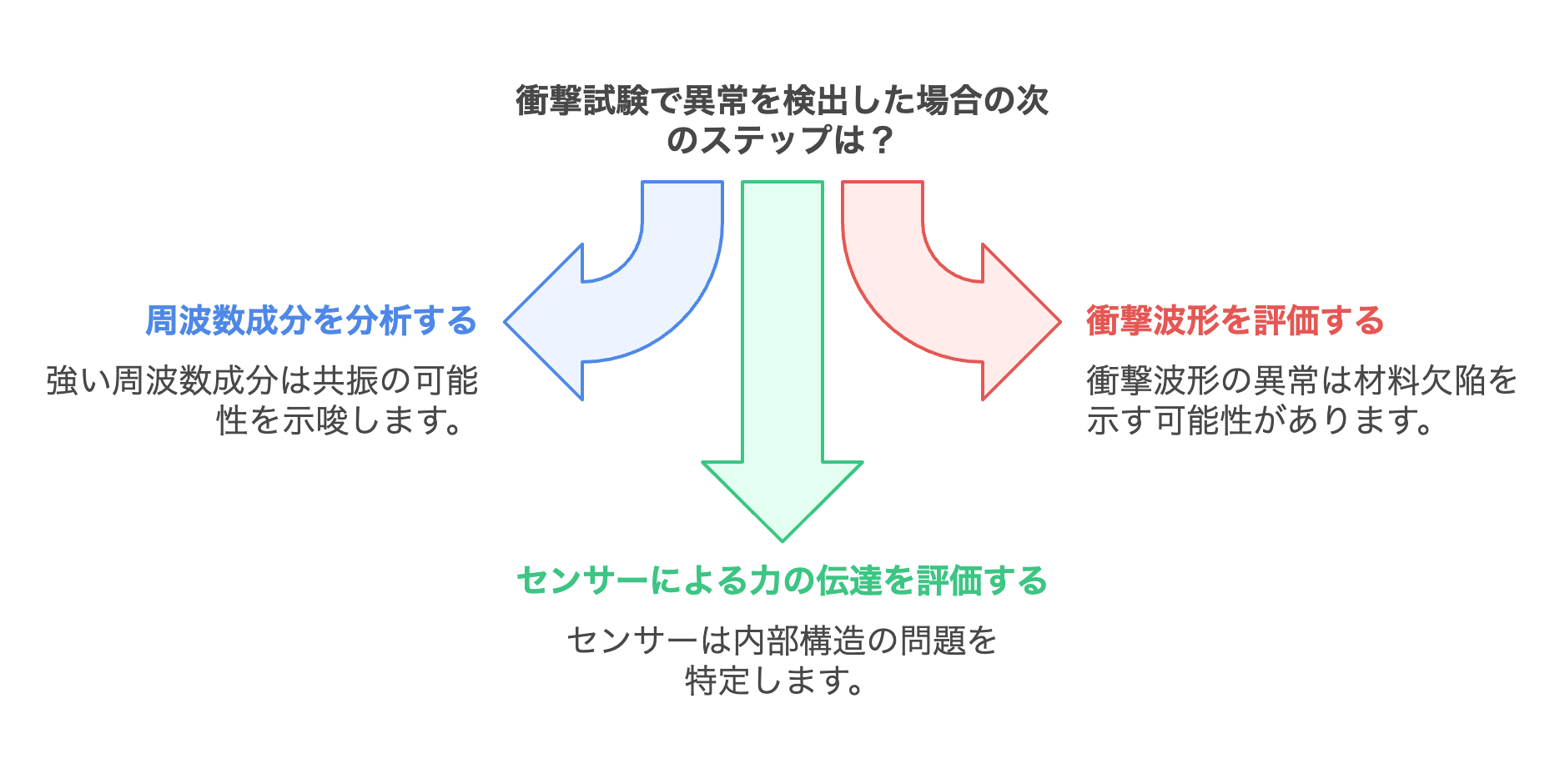
衝撃で異常が検出された場合、まず振動データの詳細分析を行います。例えば、特定の周波数成分が強い場合は共振現象の可能性があり、衝撃波形の異常は材料欠陥を示唆することがあります。打撃力検出センサーを用いることで、力の伝達状態も把握でき、内部構造の問題や組立不良による接触不良なども特定できます。
対策の立案と実施
不具合の原因特定後は、適切な対策を立案・実施します。一般的な対策とその実施例を以下に示します。 設計面では、自動車部品メーカーA社の事例が参考になります。エンジンマウントの共振による破損が発生していましたが、CAE解析を活用して補強リブの配置を最適化することで、強度を30%向上させることに成功しました。 製造プロセスの改善例としては、電機メーカーB社のケースがあります。基板実装時の半田付け条件を見直し、接合部の信頼性を向上させました。具体的には、リフロー温度プロファイルの最適化により、振動耐久性が2倍に向上しています。 材料変更による対策では、産業機器メーカーC社が、従来の汎用樹脂から制振性の高いエンジニアリングプラスチックに切り替えることで、共振による破損を解決した例があります。材料コストは増加しましたが、クレーム対応コストの削減で総合的なコストダウンを実現しています。
振動試験に関するご相談は、TMCシステムへ
振動試験でお困りの点はございませんか?
- 製品サイズに適した振動試験機の選定方法がわからない
- 試験条件の設定に不安がある
- 試験データの収集・分析を効率化したい
- 試験の自動化を検討している
など、振動試験に関するお困りごとがございましたら、まずはお気軽にご相談ください。TMCシステムでは、お客様の製品特性や試験要件に合わせた最適な試験システムをご提案いたします。また、試験条件の最適化から、データ分析、自動化システムの構築まで、幅広くサポートいたします。